Pool coping isn’t just decorative it’s a critical structural component that protects your pool’s integrity. You’ll find it serves multiple essential functions: creating a watertight barrier between your pool shell and deck, preventing water seepage, providing safe grip for swimmers, and redirecting splash-out to proper drainage. It also conceals rough edges while enhancing your pool’s aesthetic appeal. Understanding coping’s material options and installation requirements will help you enhance your pool’s performance and longevity.
Key Takeaways
- Pool coping creates a critical barrier that prevents water from seeping behind the pool shell, protecting the structural integrity.
- It provides a safe, non-slip surface with rounded edges for swimmers entering and exiting the pool.
- Coping effectively manages water drainage by directing splash-out and rainwater away from the pool structure.
- It serves as a decorative element that enhances pool aesthetics while concealing rough edges of the pool wall.
- The coping cap protects the pool structure from water damage and creates a clean, finished look around the perimeter.
Understanding Pool Coping’s Core Function

While many pool design elements are primarily aesthetic, pool coping serves both functional and decorative purposes as a critical structural component. In a functionality overview, you’ll find that coping creates an essential barrier between your pool’s structure and the surrounding deck area, preventing water from seeping behind the pool shell and causing structural damage.
Pool coping types vary, but they all serve to cap the pool wall, concealing the rough edges of your pool’s shell while providing a smooth, finished surface. You’ll notice that proper coping redirects splash-out water away from the pool’s structure and into the deck drains. It’s also designed to give swimmers a secure grip when entering or exiting the pool, making it an integral safety feature in your pool’s design.
Safety Features and Slip Resistance
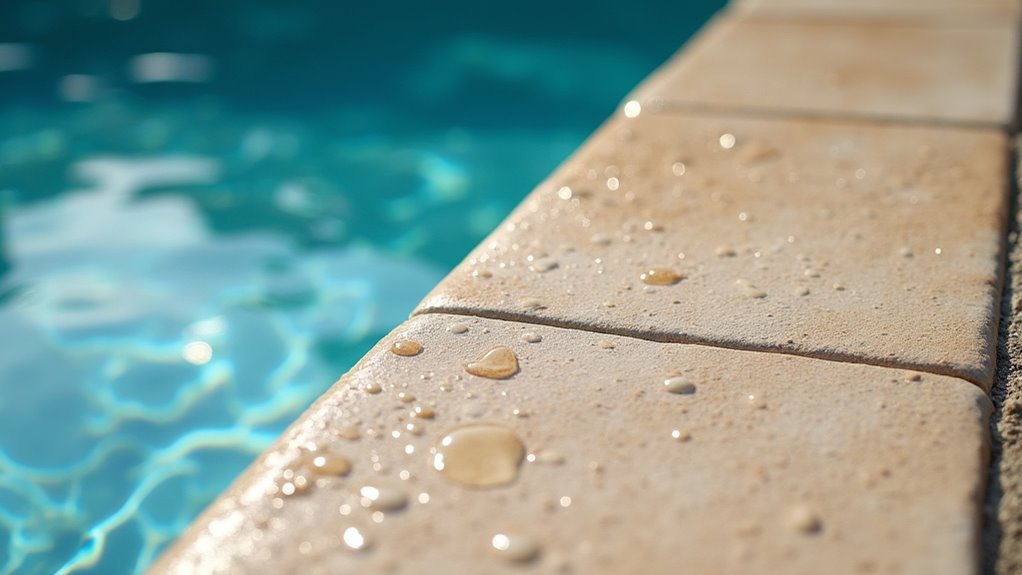
The safety-critical nature of pool coping demands precise attention to slip resistance and surface texture specifications. You’ll need to verify your pool coping meets industry-standard slip resistance ratings, typically measured by coefficient of friction (COF) testing. Quality pool coping materials should achieve a minimum COF of 0.6 for wet conditions.
Safety features extend beyond basic slip resistance. You’ll want to take into account rounded edges to prevent injuries, proper drainage channels to minimize water accumulation, and surface texturing that provides grip without being abrasive. The coping’s texture should maintain effectiveness in both dry and wet conditions, as it’s vital for preventing poolside accidents. Furthermore, you’ll need to confirm that your chosen coping material complies with local safety regulations and ADA accessibility requirements for public pools.
Structural Protection and Water Management
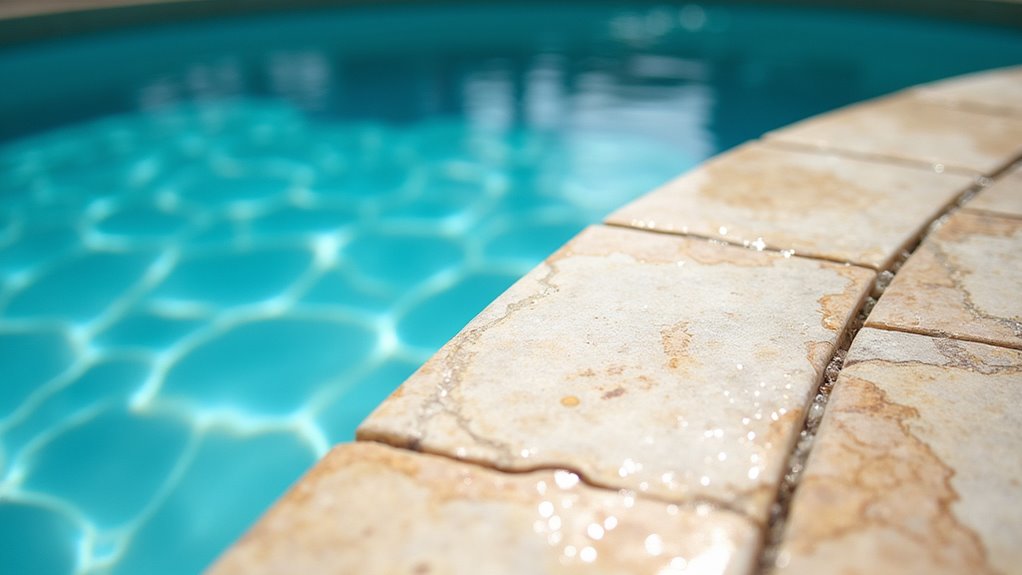
Since proper structural protection determines your pool’s longevity, pool coping plays a critical role in preventing water infiltration between the pool shell and surrounding deck. You’ll find that well-installed coping creates a watertight seal that safeguards your pool’s structural integrity by directing water away from critical junctions.
Your pool coping’s design facilitates efficient water drainage through a slight outward slope, preventing water from seeping behind the pool wall. This slope helps channel splash-out and rainwater towards designated drainage areas rather than allowing it to collect against the pool structure. You’ll notice that the coping’s overhang also creates a drip line, ensuring that water drops away from the pool wall instead of running down it, which could otherwise compromise the shell-deck connection over time.
Material Options and Their Benefits
Varied pool coping materials offer distinct advantages for your installation, with natural stone, precast concrete, and brick representing the most prevalent options. You’ll find that natural stone, including granite, limestone, and travertine, provides superior durability and a luxurious aesthetic, though it requires periodic sealing. Precast concrete alternatives deliver cost-effectiveness and versatility, featuring standardized dimensions and differing textural finishes.
When you’re selecting materials, you’ll need to take into account your climate’s freeze-thaw cycles and UV exposure. Brick coping offers traditional appeal and excellent slip resistance, while composite materials provide modern alternatives with improved weather resistance. Each material’s thermal properties affect deck comfort – natural stone typically remains cooler than concrete in direct sunlight, while engineered materials often incorporate heat-reducing technologies.
Design Impact on Pool Aesthetics
Building upon material selection, pool coping design greatly influences your pool’s visual appeal and architectural character. You’ll want to contemplate how the coping’s profile, thickness, and overhang create distinct shadow lines that define your pool’s perimeter. A bullnose edge offers soft, flowing aesthetics, while a squared edge delivers contemporary sophistication.
To achieve visual continuity, you’ll need to coordinate your coping’s design elements with your surrounding hardscape. The width and pattern of your coping can either emphasize or minimize the shift between pool and deck. Color harmony plays an essential role you can choose contrasting tones to make your pool’s edge pop, or select matching hues to create a seamless integration with your environment design. These design decisions greatly impact your pool’s complete architectural expression.
Installation Methods and Best Practices
When installing pool coping, proper preparation of the substrate forms the foundation for long-term stability. You’ll need to verify the concrete bond beam is clean, level, and free from debris before beginning the installation process.
Installation Step | Best Practice | Key Considerations |
---|---|---|
Surface Prep | Clean with pressure washer | Remove all loose material |
Mortar Application | Use 1:3 cement-sand ratio | Maintain consistent thickness |
Coping Placement | Set with slight pitch outward | Verify 1/8″ drainage slope |
Joint Treatment | Fill with flexible sealant | Allow 24-hour curing time |
Apply your mortar bed using proper installation techniques, maintaining uniform thickness throughout. You’ll want to position each coping stone with precision, verifying correct spacing and alignment. For best results, don’t rush the process – proper curing time between steps is essential for durability and longevity.
Maintenance Requirements and Longevity
To guarantee pool coping maintains its structural integrity and aesthetic appeal, you’ll need to implement a systematic maintenance routine that addresses both preventive care and periodic repairs.
Regular maintenance and timely repairs are essential safeguards for preserving your pool coping’s structural soundness and visual appeal.
Key maintenance tips and longevity strategies for pool coping include:
- Apply a penetrating sealer every 2-3 years to protect against water infiltration, UV damage, and chemical exposure, particularly for natural stone materials
- Inspect joint compounds quarterly for deterioration, replacing damaged mortar or caulking to prevent water penetration beneath the coping
- Clean surfaces monthly using pH-neutral cleaners to remove mineral deposits, algae growth, and environmental contaminants that can accelerate wear
- Monitor for crack formation or displacement, especially after freeze-thaw cycles, addressing any structural issues immediately to prevent extensive damage
Regular implementation of these practices will considerably extend your pool coping’s service life while preserving its functionality.
Cost Considerations and Budget Planning
Investing in pool coping requires careful financial planning across multiple cost dimensions, including material selection, installation complexity, and long-term maintenance expenses. Your budget allocation must factor in both upfront and recurring costs while guaranteeing quality isn’t compromised.
Cost Factor | Considerations |
---|---|
Materials | $15-75/linear ft |
Installation | $8-25/linear ft |
Maintenance | $2-5/linear ft/year |
Repairs | $10-30/linear ft |
When developing your cost estimation, you’ll need to calculate the total linear footage of your pool’s perimeter. Premium materials like natural stone will increase your initial investment but may offer better longevity. Consider requesting quotes from multiple contractors to guarantee competitive pricing, and always maintain a 10-15% contingency fund for unexpected issues during installation or future repairs.
Common Problems and Prevention Strategies
Despite proper installation, pool coping can develop several structural and aesthetic issues that require prompt attention. You’ll need to monitor for common problems and implement preventive measures to maintain your pool’s integrity and safety.
- Cracked coping often results from ground settlement or freeze-thaw cycles – seal cracks immediately with appropriate epoxy compounds to avoid water infiltration
- Water pooling on coping surfaces indicates improper drainage slope – adjust the pitch to guarantee water flows away from the pool’s edge
- Loose or separating coping stones compromise structural stability – replace deteriorated mortar and realign displaced pieces promptly
- Efflorescence (white mineral deposits) signals moisture migration through stone – apply penetrating sealers annually and maintain proper chemical balance to avert mineral buildup
Regular inspections and swift remediation of these issues will extend your pool coping’s lifespan and preserve its functionality.
Frequently Asked Questions
Can Pool Coping Be Replaced Without Draining the Entire Pool?
Yes, you can replace pool coping without draining your pool completely. You’ll need to maintain the water level just below the coping edge during the pool maintenance process. To replace the coping materials, you’ll initially remove the old coping sections, clean the exposed bond beam, and install new coping using appropriate adhesive and grout. It’s essential to guarantee proper waterproofing and sealing during installation to prevent water infiltration behind the coping.
Does Pool Coping Affect the Temperature of the Water?
Yes, pool coping can affect your water’s temperature in two significant ways. Initially, it influences heat retention by either absorbing or reflecting sunlight. Dark-colored coping materials absorb more heat and can transfer it to your pool water, while lighter colors reflect sunlight. Second, it impacts water evaporation rates at the pool’s edge – properly installed coping with the right overhang helps minimize water loss, which helps maintain consistent water temperatures.
How Long Should I Wait Before Using the Pool After Coping Installation?
You’ll need to wait at least 24-48 hours after coping installation before using your pool to guarantee proper curing and peak coping durability. For mortar-set coping, extend this waiting period to 72 hours, especially in humid conditions. During this time, don’t allow any water splashing or contact with the newly installed coping. If you’re using epoxy-based adhesives, consult your manufacturer’s specific guidelines, as curing times may vary based on environmental conditions.
Can LED Lights Be Integrated Into Pool Coping for Nighttime Illumination?
Yes, you can integrate LED lights into pool coping for stunning nighttime aesthetics. The installation requires special coping pieces with pre-built channels or housing units for LED strips. You’ll need waterproof LED systems rated for outdoor use (IP67 or higher) and proper voltage transformers. The integration can be achieved through surface-mounted strips or recessed lighting channels. Consider using RGBW LEDs for color customization and smart controllers for automated lighting schedules.
Will Pool Coping Change Color or Fade Over Time From Sunlight Exposure?
Yes, you’ll notice color fading in pool coping over time due to prolonged sunlight effects. Natural stone coping materials like limestone or travertine typically experience UV-related discoloration within 3-5 years. To minimize this, you can apply UV-resistant sealants every 2-3 years. Precast concrete coping with integral color tends to maintain its appearance longer, but you’ll still see some fading after 7-10 years of direct sun exposure.